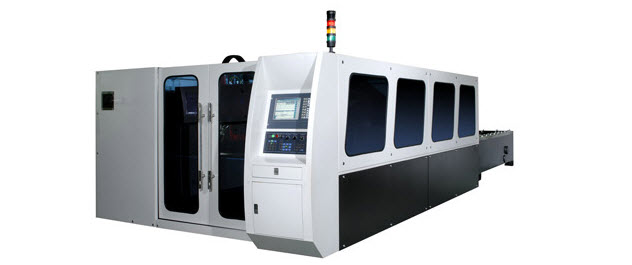
IndraMotion MTX standard
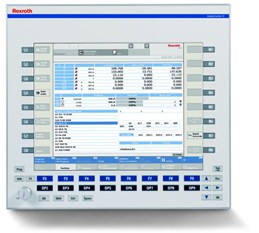
IndraMotion MTX standard – PC-based CNC system. The CNC and PLC functions are packaged as a plug-in controller in an industrial PC. Even the basic version offers outstanding performance for 8 axes, of which 2 can be used for spindle functions. Two independent CNC channels are available for process automation.
IndraControl VSP industrial PCs can be integrated seamlessly into the IT network landscape in modern production environments – including a complete package for operation and programming and fast communications ports.
Machining Technologies |
Turning |
Milling |
Drilling |
Grinding |
Nibbeling, Laser cutting |
Forming |

Axis control |
Max. 8 axes |
Max. 2 axes on each spindel |
2 independant circuits |
Max. 4 interpolating axes per circuit |
Linear axes, endless linear axes |
Round axes |
Endless rotating round axes |
Hirth axes |
Spindel/C axis change-over |
Max. 4 gantry axes per circuit 2 |
Max. 4 synchronized groups per circuit 1,2 |
circuit-spanning axis transfer |
Cam |
Software terminating switch |
Master spinndel synchronisation 1,2 |
Integrated safety technology cat. 3 according to DIN 954-1 (secure grip, safe reduced speed, secure end possitions) 6 |

Interpolation functions |
Linear interpolation |
Linear interpolation with/without accurate stop |
Circular interpolation with radius and center programming, helix interpolation |
Circular interpolation with tangential entrance |
Threading drilling without balancing chucker |
Threading drilling |
max. 30 NC sets projection, look ahead with jerk limiting |
6 ms interpolation cycle time, min. with 8 axes |
Spline interpolation, C1 + C2 continuous, cubic splines, B-splines, NURBS 1,2 |
Nanometer resolution |

Feed functions |
Feed in mm/min oder inch/min |
time programming |
Feed per rotation |
Constant cutting speed 1 |
Drive to fixed stop |
Torque reduction |

Adjustments and corrections |
Mirroring, scaling, turning |
Zero offset |
Corrections and zero offsets programmable using PLC |
Corrections and zero offsets programmable using CPL |
Placements (Frames) 2 |
2D path corrections |
Path correction with planar transition |
Tangential tool guidance |

Tool management |
Integrated, flexible tool management |
Configurable tool database |
Freely definiable tool corrections (length, radius, cutting placement correction, user data) |
Additive tool corrections(D-corrections) |
Access to tool data from the PLC |
Access to tool data from the CNC |

CNC programming |
Partial program creation according to DIN ISO 66025/EIA274 |
HLL programming, CPL customer programming language |
Graphic NC programming 4,5 |
Graphic NC simulation 4,5 |
64 MB CNC user memory |
8 MB statistical memory |
Max. partial program size dependent on PC hard drive |

Technology cycles |
Drilling 1,2 |
Turning 1,4 |
Milling 2,5 |

Functions |
Dwell time in seconds |
Acceleration programming, KV programming |
Referencing over NC programm |
Absolut measurement, relative measurement |
Change-over inch/mm |
Sensor, stationary/flying measuring |
Read process and drive data with SERCOS interface |
Curves and phases |
Laser power control |
Digitalizing |
NC block default setting from PLC |

Support for operator intervention |
Configurable operation images |
Cycle header/input aid OEM cycles |
Block feed/block search run |
Dry Run |
Removal und NC block restart on the outline |

PLC programming |
Integrated PLC: IndraLogic |
Programming languages IEC61131-3 (AWL, KOP, FUP, ST, AS) |
8 MB PLC program memory |
optional 8/8 high speed inputs/outputs |
8KB per fieldbus inputs/outputs |
typ. PLC processing time 0,6ms per 1.000 commands |
Multitasking |
Max. 16 PLC tasks |

Diagnosis and start-up tool |
Integrated, system comprehensive engineering framework IndraWorks |
Automatic system supervision |
Indication and error messages in plain text |
Integrated drive projection |
Drive oszilloscope |
Integrated PLC projection |
Logic analyzer |
optional remote diagnosis |

Openness |
Configurable user interfaces with all standard functions |
Projectable, user defined operator images |
Adaption and integration over standardized interfaces (OPC, XML, ActiveX, .NET) |

Control hardware and interfaces |
CPU: IndraControl P40 |
Digitale drive interface SERCOS interface, 2 - 16 Mbaud |
Profibus DP, 12 Mbaud |
Ethernet, 100 MBit |

Software and hardware |
Operating system Windows XP |
optional panel PC IndraControl VSP 16 |
optional panel PC IndraControl VSP 40 |
optional panel PC IndraControl VSB 40 |

1) Requirement technology package "Turning 1"
2) Requirement technology package "Milling 1"
3) Requirement technology package "Milling 2"
4) Requirement shop programming "Turning"
5) Requirement shop programming "Milling"
6) Option in connection with IndraDrive